ASTM D395
Rubber Compression Set
Test Method A Compression Fixture
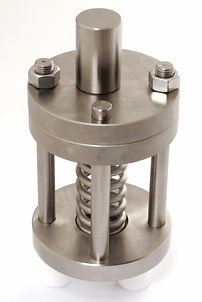
Test Method B Compression Fixture


ASTM D395 - Standard Test Methods for Rubber Property—Compression Set - PDF
Method A, B, and C Explained with Fixture Requirements and Test Setup
ASTM D395 is the standard test method used to determine the compression set of rubber materials. This test evaluates how well a rubber sample returns to its original thickness after being compressed for a fixed period under specific environmental conditions.
Compression set is an essential property for rubber materials used in gaskets, seals, O-rings, and other applications where the ability to maintain shape under load is critical.
ASTM D395 defines three methods:
-
Method A – Compression set under constant force in air
-
Method B – Compression set under constant deflection in air
-
Method C – Compression set under constant deflection in air using a compression device (non-standardized, but often used in product testing or long-term research)
What is Compression Set?
Compression set measures the permanent deformation a rubber material retains after being compressed and allowed to recover. It's expressed as a percentage of the original deflection. Lower values indicate better elastic recovery.
Compression Set (%) is calculated as:
CS = [(t₀ - t₁) / (t₀ - tₛ)] × 100
Where:
-
t₀ = original specimen thickness
-
t₁ = final specimen thickness after recovery
-
tₛ = spacer thickness (only applicable for Method B & C)
Method A – Constant Force in Air
Purpose: Simulates conditions where a rubber part is compressed by a constant force (spring or bolt pressure).
Specimen:
-
One cylindrical test piece, typically 12.5 mm thick and 29 mm in diameter
-
Thickness tolerance: ±0.5 mm
Test Setup:
-
A compression fixture with two metal plates and a loading bolt/nut arrangement.
-
The rubber specimen is compressed between the plates using a measured force, usually applied via calibrated weights or a universal testing machine with a force control function.
Procedure:
-
Measure initial thickness (t₀).
-
Apply constant force (e.g., 1.8 kN) using compression fixture.
-
Place the assembly in an oven at 70°C to 100°C for 22 to 70 hours.
-
After aging, remove and allow the sample to recover at room temperature for 30 minutes.
-
Measure final thickness (t₁) and calculate compression set.
Notes: This method is less commonly used than Method B, as constant-force setups are harder to maintain uniformly.
Method B – Constant Deflection in Air
Purpose: Most commonly used to evaluate sealing materials (O-rings, gaskets) under long-term load.
Specimen:
-
Same as Method A (12.5 mm thick × 29 mm diameter)
Test Setup:
-
A compression set fixture designed to apply a constant deflection, typically 25% of the specimen’s original thickness.
-
Spacers (typically steel) ensure consistent deflection.
-
The fixture must maintain deflection during heat exposure.
Procedure:
-
Measure initial thickness (t₀).
-
Insert the specimen between plates with spacers to achieve a 25% compression.
-
Place in an oven at the required test temperature for 22 to 70 hours.
-
Remove and allow the specimen to cool for 30 minutes.
-
Remove from the fixture and measure the final thickness (t₁).
-
Use the formula to calculate compression set.
Fixtures:
These fixtures typically include:
-
Two flat plates (top and bottom)
-
Threaded bolts and nuts
-
Precision spacer bars or pins
The fixture must resist warping during heating, so stainless steel or hardened aluminum is ideal.
Method C – Custom Deflection in Air (Non-Standard Setup)
Purpose: Used in R&D and product testing where part geometry doesn’t allow standard specimens.
Specimen:
-
Custom shape or real product component (e.g., actual O-ring or gasket section)
Setup:
-
Test conducted using non-standardized fixtures, often designed to mimic the actual application.
-
Can use precision jigs or devices that simulate the installed condition of a component.
Procedure:
Follows the same general steps as Method B, except the fixture and compression amount are specific to the real-world application. Recovery and measurement protocols remain similar.
Important: Method C is not part of the formal ASTM D395 standard but is referenced in practice for product-specific compression set evaluations.
Summary Table
MethodCompression TypeSpecimenFixture RequirementTypical Use
AConstant ForceCylindrical discLoad frame or fixture with weightsSpring-loaded gaskets
BConstant DeflectionCylindrical discPrecision spacer fixtureSealing applications (O-rings)
CConstant DeflectionCustom shapeApplication-specific setupR&D, product simulation
Final Thoughts
When performing ASTM D395 testing, accuracy in fixture setup and environmental control are essential.
Whether you're certifying material performance for aerospace seals or testing industrial O-rings, a properly configured compression set test gives you the data you need to evaluate long-term elasticity and durability.
If you need help sourcing or customizing a compression set fixture for ASTM D395 testing, we offer ready-to-use kits and custom setups that are compatible with most lab ovens and testing environments.